Supercritical CO2 Extraction
During supercritical fluid extraction with CO2 components are separated from a solid or liquid carrier material by using supercritical CO2 as solvent.
For many applications CO2 has well-suited solvent properties which can be easily controlled by varying the pressure and temperature. In addition carbon dioxide in the supercritical state has a very low viscosity and no interfacial tension. Therefore it can penetrate well into complex structures and materials. These properties make it suitable for many different processes.
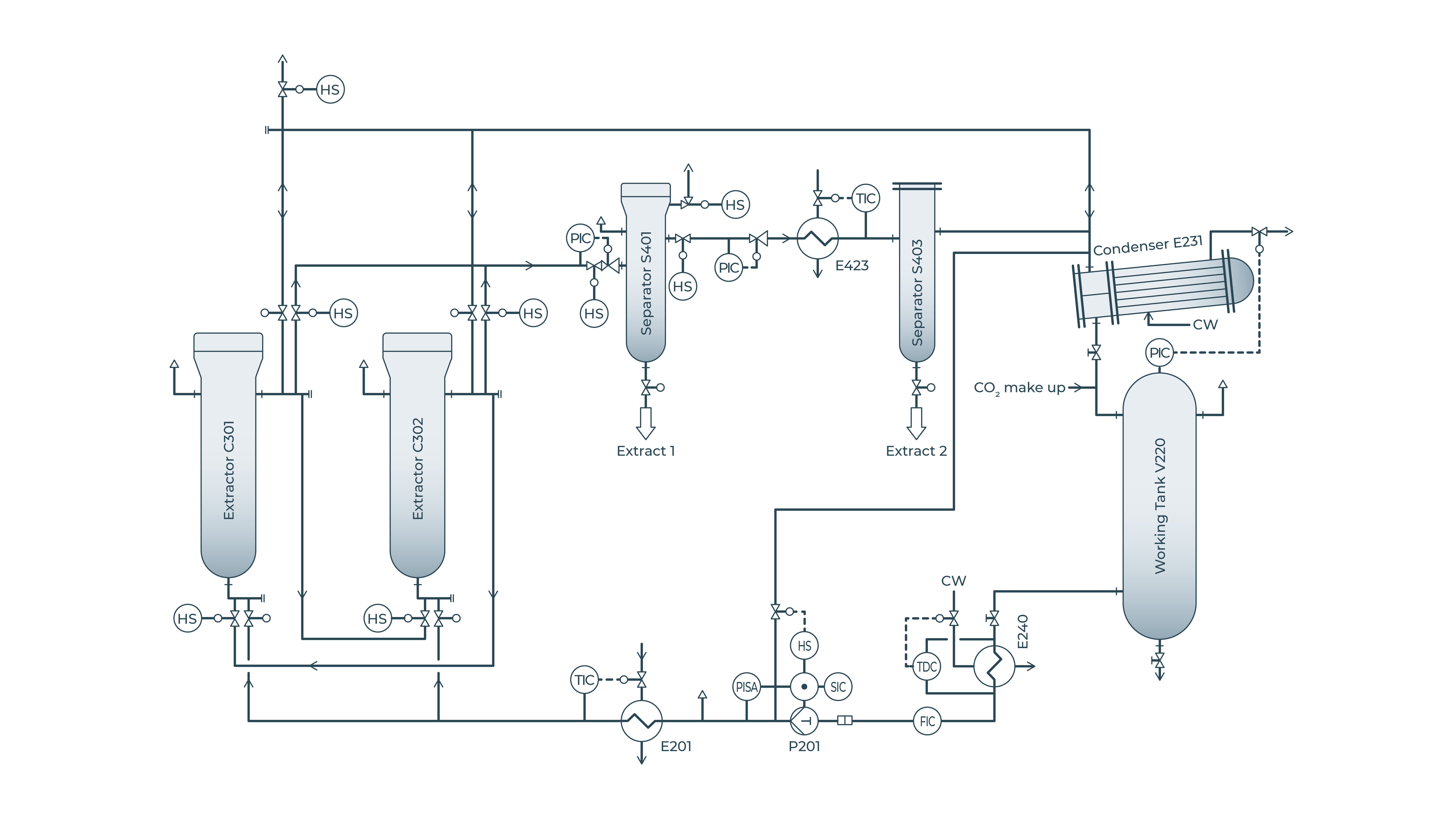
A typical supercritical CO2 extraction system is shown schematically in the picture above. The process starts at the working tank, where the CO2 is stored for the operation. It is then compressed in a high-pressure pump and brought to the desired extraction temperature. Afterwards it is directed into one of the extraction vessels in which the carrier material is located. The extractors are equipped with quick opening closures to allow easy and safe filling and discharging. Solid raw materials are typically fed into the extractor by means of a basket. Several extraction vessels can be combined to a functional system so that extraction can be carried out on a continuous basis despite the batch operation of the extractors. After leaving the extractors the loaded carbon dioxide reaches the separators where the change in pressure and / or temperature creates conditions in which the extract separates from the carbon dioxide. The extract can then be collected at the bottom of the separators. This is also where the solvent properties of CO2 allow a fractionation of the extract into different separators. In the last separator the CO2 is usually expanded to a gas state to remove all the remaining compounds. This pressure level is of importance since energy intensive recompression should be avoided. After separation the gas is liquified in a condenser and fed back into the working tank. It can now be used again.
- CO2 is inexpensive, not combustible, not explosive, germicidal, free of bacteria, selective and mobile
- Heat sensitive materials are gently treated
- Products and residues are solvent-free
- Fragrances and aromas remain unchanged
- An excellent flavour profile can be achieved for oils
- Pure extracts are produced with few process steps
- The solvating power can be changed (conditions, or the use of modifiers)
- Selective extraction and fractionated separation is possible
- CO2 is recycled within the plant, is physiologically harmless and does not cause environmental problems like some conventional solvents
In general the more volatile a compound the higher its solubility in CO2 (supercritical and fluid) and the easier the supercritical fluid extraction process. Therefore the below mentioned list serves as first indication. The properties of CO2 and the solubilities of the compounds can be modified by injection of co-solvents and varying temperature and pressure.
Easy soluble | Soluble | Unsoluble |
---|---|---|
|
|
|
|
|
|
|
|
|
|
| |
|
| |
|
- Food industry
- Decaffeination of coffee & tea
- Extraction of hops, herbs & spices
- Recovery of flavours, antioxidants
- Extraction of special oils
- Deoiling of press cakes
- Cleaning rice
- Pharmaceutical industry
- Extraction of herbal medicines
- Refining of pharmaceuticals
- Cosmetic industry
- Active ingredients for cosmeceutical applications
- Fragrances
- Other applications
- Cleaning of cork
- Impregnation of wood
- Chemical reactions
- Particle formation
- Cleaning
- Sterilization
Our Services
We are a full-service provider for developing supercritical CO2 extraction projects from the initial idea to the startup of a commercial plant including the delivery of the required equipment:
- Development of new supercritical processes for the extraction of the requested material
- Process validation based on the idea of our customers and results from research projects in our own R&D and pilot plants
- Scale up testing on in-house pilot plants
- Concepting and engineering of industrial scale extraction plants based on customer’s requirements and test results
- Design and supply of state of the art extraction related process equipment and machinery
- Supervision of erection and commissioning
- Training of operators
- Long term support